10 main steps towards the implementation of the international standard ISO 9001:2015 in the textile sector
- Vusala Javadova
- 29.04.2025
- 18
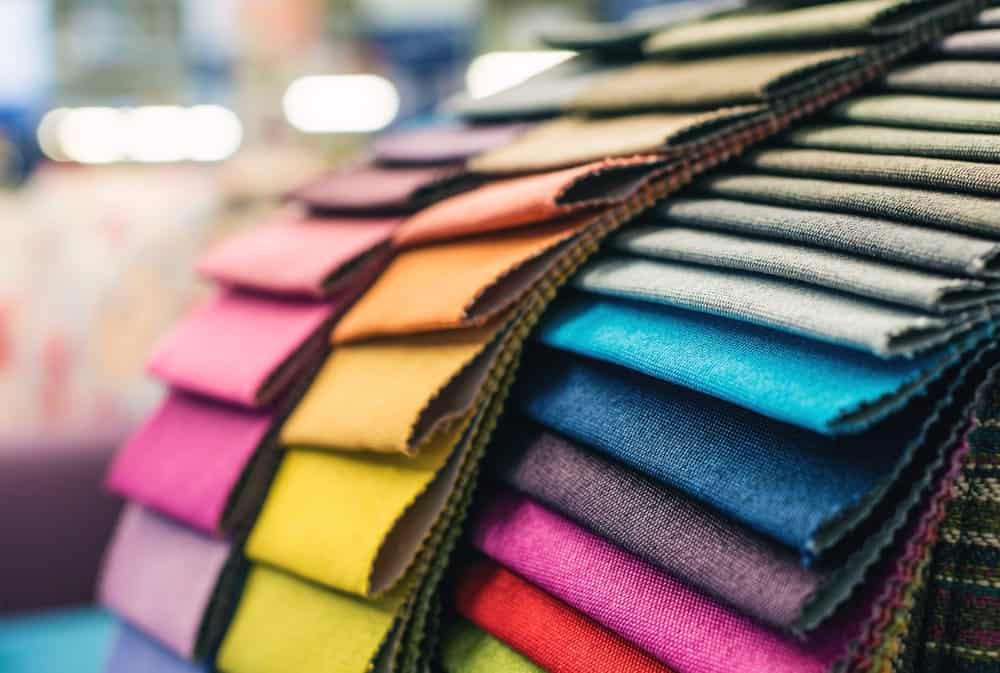
Step 1: Assessment of the current situation
The stage of assessing the current state (gap analysis) before starting the application of ISO 9001 is one of the most important steps. At this stage, textiles
It is designed to identify differences between ISO 9001 requirements and the current situation in the enterprise and form the basis of the application. The stage of assessing the current situation (GapAnalysis) before starting the application of the standard is one of the most important. At this stage, the differences between the requirements of the standard and the current situation are identified and the basis of the application is formed.
1.1. The sequence and interrelation of existing processes is determined.
Receiving and storing parts at the warehouse;
Cut;
Paint;
Sewing;
Quality Control;
Iron and packaging;
Sale.
The inputs, outputs, responsible persons, and equipment used are recorded for each process.
1.2. Verification of the level of documentation: available documents are collected and compared with the requirements of ISO 9001.
1.3. Assessment of the level of training of experienced employees: the level of training of employees in understanding processes and quality is assessed.
1.4. Quality indicators study: analyzes the percentage of nonconforming products over the past 6 or 12 months, the number of customer complaints, processing cases, the number of overdue orders, and production losses.
1.5. Nonconformities and risks are assessed: the existing nonconformities and their main causes are identified.
Step 2: Ensure leadership commitment
Paragraph 5 of the ISO 9001:2015 standard-the manual directly emphasizes the responsibility of management.Management should lead the implementation, maintenance and continuous development of the quality management system.
2.1.Definition of the quality area: management should develop a quality policy in accordance with the overall objectives and strategic plan.
2.2. The requirements of the ISO 9001 standard should ensure its integration into business processes.
2.3. The active participation of management in all ongoing processes should be ensured.
2.4. Relevant roles and responsibilities – who will do what when applying ISO 9001? Job responsibilities for each category should be documented and
it should be specified in the organizational structure of the enterprise.
2.5. Building a quality culture - a “suggestion box” should be developed to make suggestions for improving the quality management system.
2.6. Performance monitoring: Management should regularly check quality indicators and approve a plan for the development of weaknesses.
Step 3: Develop a project plan
Develop a clear action plan and schedule for the construction and certification of a quality management system (QMS) in accordance with the requirements of the ISO 9001 standard.
3.1. Determining the scope of the project – which sections will be included in the scope of the ISO 9001 standard. Example: dyeing factory, sewing factory,
Cutting and selling area
3.2. Carrying out the division of responsibilities and drawing up a schedule indicating the stages of the project: a timeline is being developed (for example, 6-8 months) indicating the stages of the project:
The duration of the project varies depending on the scope of the standard and the number of employees.
3.3. Main tasks and stages – the purpose of each stage and the expected result should be defined.
3.4. Resource planning: planning of human, technical and financial resources
3.5.Identification of risks and delays: As with every project, scenarios are established for delays and risks are assessed.
3.6. Reporting mechanism: management should be regularly informed about the progress of the project.
Step 4: Informing and training staff
The purpose of this step is to inform employees about ISO 9001, understand their role in the system, and ensure that their activities are consistent with the processes.
culture of quality.
4.1. Identification of training needs: First, it is determined which personnel in various fields need training in which subjects.
4.2. Organization of information sessions in simple language, tell all employees about the main concepts and objectives of ISO 9001
An information session is being organized.
4.3. Process-specific training Employees receive hands-on training in procedures, job descriptions, and records relevant to their field:
Example: parts acceptance standard, quality criteria
1st quality, 2nd quality, and 2a; sewing sequence and quality points, recycling management, proper daily record keeping (checklist,
mold quality control)
4.4. Preparation of educational materials
4.5. Learning Assessment: A simple test or observation method is used to evaluate the results after learning.
4.6. Remuneration and motivation: encouraging employees with motivational methods who actively participate in training and act in accordance with processes.
Step 5: Document preparation
5.1. In the ISO 9001 application, the “step 5: document preparation” stage is the main structure that ensures the stability and traceability of the system. In particular, in the textile industry, proper documentation is crucial because the processes are multifaceted and operational.
The goal is to document the quality management system in accordance with the requirements of the ISO 9001:2015 standard, standardize processes, ensure traceability and control.The main types of documents are:
Quality policy and objectives;
Procedures;
Work instructions;
Registration forms.
5.2. Document Management -each document must have a version number, date, the person who prepared it, and the person who approved it. Outdated documents
should be put out of use, and only controlled documents should remain in circulation.
5.3. Ensuring confidentiality and accessibility – each document should be accessible only to interested parties. For example, internal audit protocols are available only to the board of directors.
it can be opened, but the equipment manual must be open to each operator.
Step 6: Implementing processes
Process implementation is the stage at which a system built with documentation begins to be applied in a real work environment. This stage ensures that employees work in accordance with the new system, and is a key opportunity to check the effectiveness of the system. The documentation established in the ISO 9001 system (procedure, instructions,
form, etc.) to implement their integration into real operations and ensure that employees carry out their daily activities in accordance with these rules
The main stages of the system implementation phase are:
6.1. Pilot application: one production area is taken and applied.For example, only a garment factory starts working with documents on the 1st lane or by selecting a section of the spare parts warehouse. At this stage, it is checked:
Are the procedures suitable for surgery?
Do employees apply the procedures correctly?
Are there any misunderstandings or difficulties with applying the procedures?
The pilot phase may last 1-2 weeks.
6.2. Compliance of the main processes with the system
6.3. Staff monitoring – the quality control team must constantly monitor the field and provide support to employees in submitting documents.
6.4. Making corrections – procedures should be reviewed if there are difficulties or inconsistencies in the documentation or instructions in the process
, and it should be simplified and unnecessary details in the forms used should be removed.
6.5. General application of the system-After successful completion of the pilot application, the system is applied in all areas-textiles, paint, cutting, sewing, ironing, packaging, labeling, warehousing, and logistics.
6.6.Verification of the conformity of daily activities with documentation – the members of the quality control team verify the conformity of daily activities with documentation
, he must verify its implementation. Example: Are quality control checks carried out every day? Are nonconformities being reported? Are the steps specified in the procedure applied in the production process?
Step 7: Conducting an internal audit
Conducting an internal audit is an important step in verifying the compliance of applied processes with standards and internal requirements. This step identifies gaps in the system, areas for improvement, and inconsistencies between actual operations and documentation.
7.1. Development of an audit plan: audits should be conducted systematically and systematically. The plan specifies the frequency of the audit, the scope, and the responsible persons.,
The dates, sections, and the name of the auditors, as well as the surname, are indicated.
7.2.Preparation of the audit checklist: Before proceeding with the audit, it is necessary to prepare a checklist in accordance with the procedures applicable to the standards of the area in which we will conduct the audit.
7.3. Conducting an audit -the auditor conducts an audit by observing, verifying documents and interviewing staff in the relevant department on a selected date.Records are being kept.
The compliance level of the processes is grouped according to the criteria specified in the "internal audit" procedure.
7.4. Preparation of an audit report - after completion of the internal audit, the results are presented to management in the form of a formalized report.
7.5. Implementation of corrective actions – corrective or preventive actions are planned and implemented in relation to all inconsistencies identified as a result of the audit
. This has been done.
Step 8: Leadership Analysis
8.1. The purpose of the management analysis is a formal assessment of system performance in accordance with clause 9.3 of the ISO 9001:2015 standard.,
making managerial decisions based on inconsistencies, opportunities and risks, and reviewing strategic and quality objectives